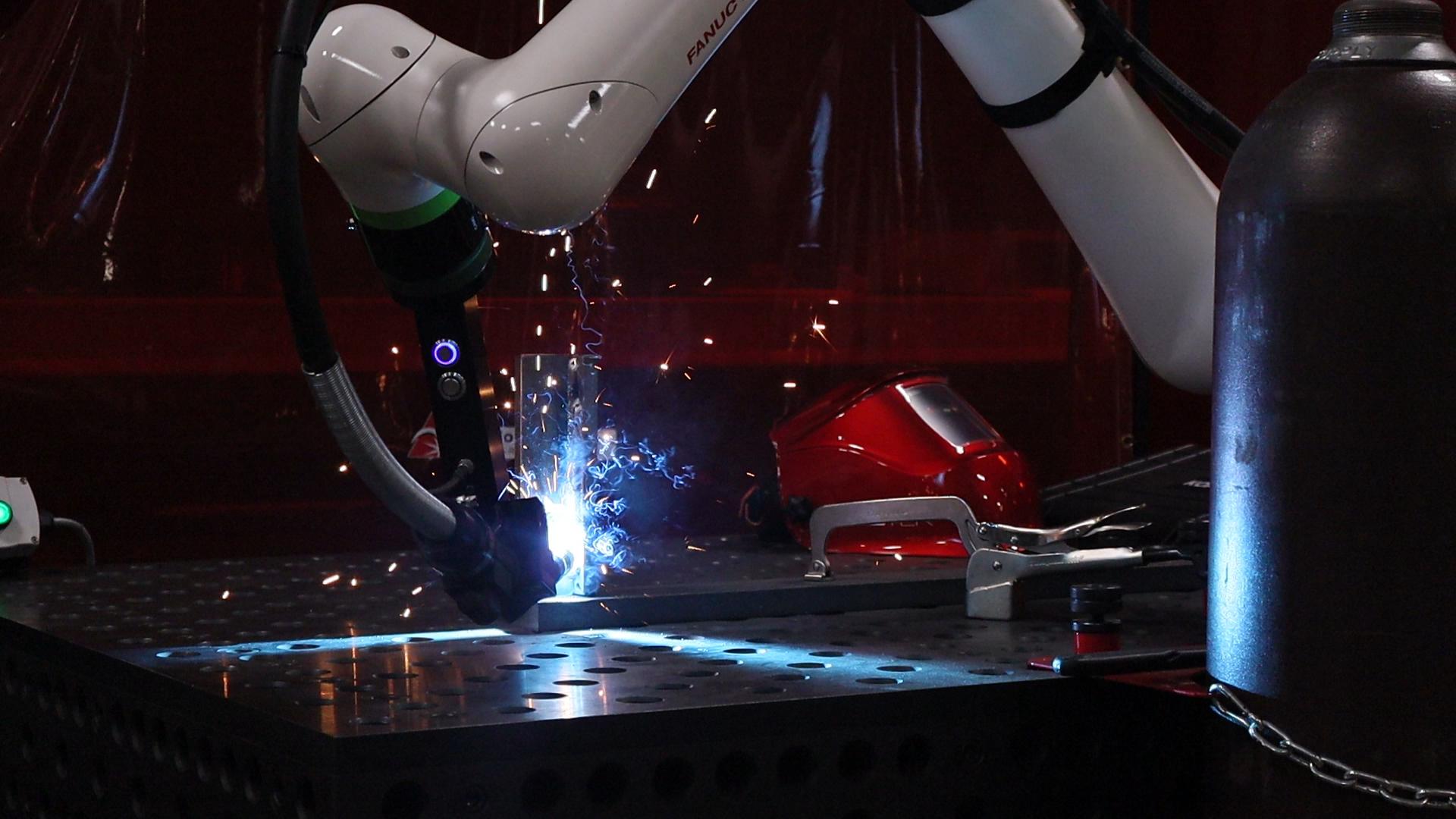
How Cobots Are Doubling Welding Efficiency for Fabricators
Turning Tables for the U.S. Fabrication Industry
Fabrication companies across industries like structural steel, shipbuilding, automotive, and oil and gas faced a harsh reality: demand for skilled welders far outpaced supply. For small shops with just five employees to large-scale operations, challenges including inconsistent weld quality, rising costs, and tight deadlines threatened their ability to stay competitive.
This struggle alone begged the question: how could these businesses produce more, maintain quality, and keep costs in check without enough skilled labor?
The answer? Collaborative robots, AKA cobots, offering a practical, affordable pathway to automated welding.
Too Much to Do, Too Few Hands
Labor shortages made finding skilled welders nearly impossible, leaving fabrication shops stretched thin. Welders on the job were overwhelmed with long hours spent over hot arcs, leading to burnout and uneven quality. These issues created a ripple effect: rework, missed deadlines, and strained budgets. The old school, manual approach wasn’t keeping up with current demands. A tall order to fill, the ideal solution required checking several boxes:
- Deliver high-quality welds consistently.
- Cut costs across materials and labor.
- Meet tight deadlines without increasing staff numbers.
- Reduce the need for extensive welding expertise.
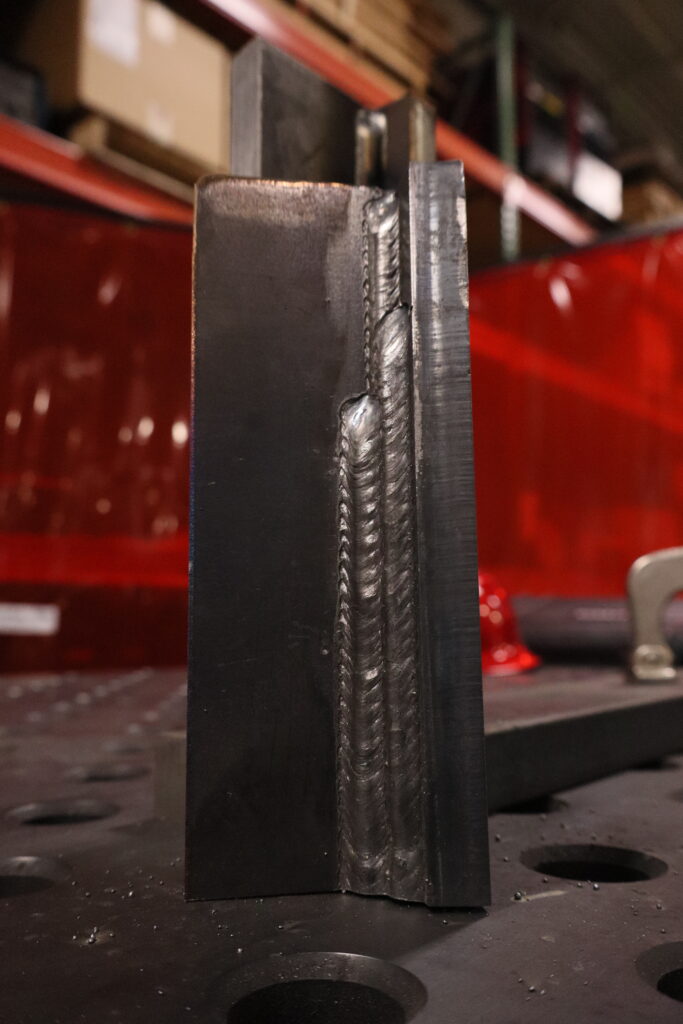
Cobots Bring Reliable, Cost-Effective Automation to Fabricators
To help fabricators turn the tide, we introduced the Fanuc CRX and Abicor Binzel iBOTone cobots for welding applications. These robotic welders brought reliability, precision, and affordability to businesses looking for a competitive edge.
The Technology at Work
- Fanuc CRX Arms: CRX10iA-L and CR25iA models paired with Lincoln Electric R450 welders.
- Abicor Binzel iBOTone Arms: Integrated with SKS welders for specialized applications.
Customized to Fit
Every cobot install was tailored to the specific criteria of their designated shop.
- Mounting Options: Tables, carts, or pedestals to suit various workflows.
- Cooling Setups: Water or air-cooled configurations for specific welding environments.
- Weld Wire Compatibility: Spool or drum options in multiple sizes.
- Custom Fixtures: Designed to optimize welding for specific part geometries.
Customer Collaboration is Key
We partnered closely with our customers at every stage.
- Demos: Hands-on previews showed cobots in action before purchase.
- Testing: Cobots underwent comprehensive evaluations before delivery.
- Tooling Reviews: Meetings ensured each robotic welding tool fit into existing customer workflows.
- Training: Operators learned cobot operation in just four hours on-site.
- Success Kickstart: Customer began running production parts on day one of cobot delivery.
From Setup to Success: The Measurable Impact of Cobots
Integrating cobots delivered measurable benefits across the board:
Production Rates Doubled
Fabricators saw their output increase twofold compared to manual welding, meeting demand without expanding their workforce.
Cost Savings and Efficiency
- Material Savings: Optimized weld sizes reduced wire and shielding gas usage.
- Less Rework: Cleaner welds meant fewer grinding pads and reduced cleanup time.
- Batch Workflow: Parts produced in batches allowed smoother stock management and quicker turnarounds.
Better Working Conditions
Operators transitioned from physically taxing welding tasks to overseeing cobots, reducing fatigue. This opened a wide door of growth capacity thanks to improving efficiency. Once everything was up and running, our customers immediately noted:
- Increased production capacity without adding staff.
- The ability to enter into cost-sensitive markets, which were previously impossible to access.
Solving Complex Welding Challenges with Customized Solutions
Some customers provided low-quality parts that required fixture adjustments and weld program fine-tuning. Our mechanical engineers worked alongside customers’ shops to address these issues. In the end, the investment in cobots had optimal results even in challenging situations.
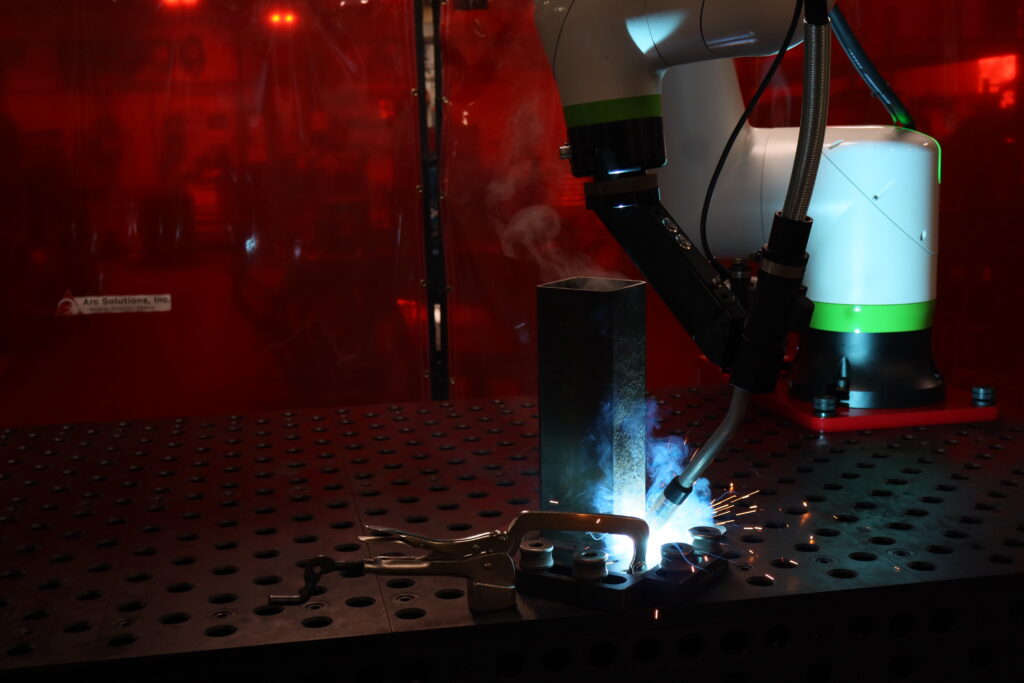
Don’t just take our word for it—hear what one of our satisfied customers has to say!
At C&C Fabrication, our experience with Arc Solutions has been exceptional. We recently leased a collaborative robot (Cobot) from them, and it has made a significant impact on our operations. From the beginning, the team at Arc Solutions worked closely with us to design, build, and program the necessary fixtures tailored to our specific needs. Their expertise was evident, and they provided comprehensive support both remote and in person, ensuring that we had everything we needed for a smooth integration. Since implementing the Cobot, we have seen a marked increase in our production capacity. It has taken over the welding of redundant parts that our employees were less enthusiastic about, allowing our team to focus on more complex tasks. The Cobot has operated reliably and effectively, proving to be a valuable addition to our workflow. We appreciate the commitment of Arc Solutions to our success and look forward to continuing our partnership. Their innovative solutions have truly enhanced our efficiency at C&C Fabrication.–Jordan Guess, General Manager at C&C Fabrication
Empowering Fabricators to Meet Demand and Grow Seamlessly
With cobots from Arc Solutions, fabrication shops were able to tackle labor shortages, meet demand, and reduce costs while maintaining high-quality standards. These automated welding solutions gave our customers the ability to grow their businesses without adding strain on their workforce.
If your shop is facing similar challenges, the introduction of welding automation with cobots may be your one-way ticket to streamlined operations – and profit. Schedule a demo today and learn how to achieve these results for your own business goals.
Cobot Request a Demo Form
Back to blog