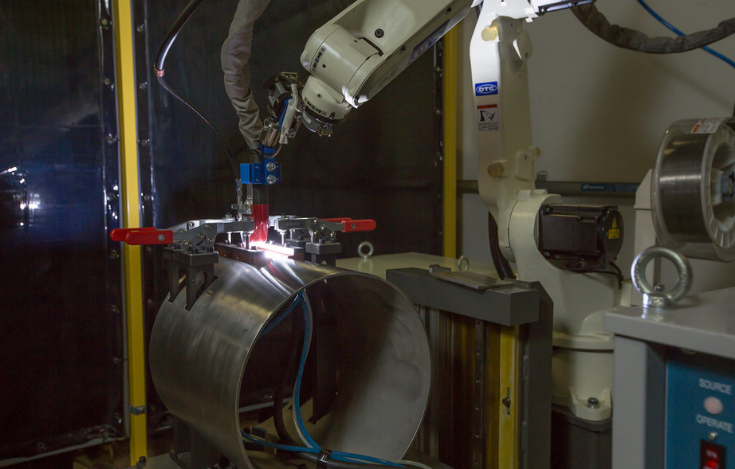
Increasing Existing Robot Efficiency
Robotic Welding: Maximizing Efficiency in Manufacturing Facilities
Manufacturing facilities have increasingly integrated welding robots into their production processes to improve efficiencies and generate more profits. With the use of robotic welders, companies can produce more products using the same resources. However, it’s not enough to simply have a robot in place. Companies need to focus on increasing robot speeds and decreasing cycle times to maximize their output.
Cycle times are measured by timing how long it takes to load a part, have the work done to it (i.e., welded), and then unload it. By reducing the cycle time, the robot can process more parts in the same amount of time, thereby increasing production. For example, reducing the cycle time by just a few tenths of a second per part can result in significant gains over time.
In this article, we will explore various ideas to increase robotic welding speeds and decrease cycle times. By implementing these ideas, companies can maximize their production output and generate more profits. But first, we’ll review the benefits robots bring to production facilities at a foundational level.
The Benefits Of Robotic Welding
Robotic welding is a great investment for manufacturing facilities because it offers numerous benefits, including increased accuracy, consistency, and productivity. Welding robots are designed to make the same precise welds over and over again, ensuring that the finished product is of the highest quality. Unlike human welders, robots do not suffer from fatigue or distractions, which means that they can maintain a high level of accuracy and consistency throughout the day.
Another significant benefit of robotic welding is increased productivity. Welding robots can work continuously, 24/7 if needed, and can complete welds much faster than a human welder. This means that more work can be completed in a shorter amount of time, increasing the overall productivity of the facility. Additionally, robotic welding can help reduce labor costs since one operator can oversee multiple robots at the same time.
In addition to accuracy, consistency, and productivity, robotic welding is also beneficial for the safety of workers. Welding can be a dangerous job, especially when it involves high temperatures, fumes, and hazardous materials. By using welding robots, companies can reduce the risk of accidents and injuries to their workers. Welding robots can withstand dangerous environments where it would be hazardous for humans to work, such as tight spaces or areas with harmful chemicals or radiation. This makes them a great addition to manufacturing facilities looking to increase efficiency.
So, how can a manufacturing facility that already has robots continue to achieve maximal efficiency? It all starts with understanding the physiology of welding automation at its core.
The Physiology Of Welding Automation
Welding automation systems can have both positive and negative impacts on workers. When used correctly, automation can make jobs and lives easier, while increasing productivity and reducing errors. However, if automation is not implemented properly, it can demoralize workers by taking away their jobs or making them feel unimportant.
To ensure that automation is being used effectively, it is important to maintain a 1:1 ratio between the amount of work being done by the robot and the operator. This means that while the robot is performing a task, the operator should have a task to perform as well. Additionally, factories have found that slowing down equipment to match operator speeds can actually increase production rates by allowing operators to keep up with the pace of the work being performed. The remainder of this article is for the opposite problem and is focused on speeding up the robot so that the operator isn’t wasting time waiting for the robot.
Know Your Parts
It is important to double-check that the robot is not being taught a strange path or a slower speed on purpose. If this is the case, the robot may not be performing at its optimal speed or efficiency. Manufacturers should speak with the appropriate parties, such as engineers or robotic programmers who originally wrote the program, to ensure that the robot is functioning properly. Having a reliable welding automation specialist on your side will keep business running smoothly.
Manual Welding vs. Robotic Welding
While manual welding has been the standard for decades, robotic welding is becoming increasingly popular due to its efficiency and cost-effectiveness. Manual welding requires skilled labor and is often more time-consuming than robotic welding. Human welders may also be more susceptible to errors, leading to the need for rework, which can be time-consuming and costly.
Robotic welding, on the other hand, can perform welds much faster and with higher accuracy than manual welding. Welding robots can also work continuously without breaks or distractions, which means that more work can be completed in a shorter amount of time. While the initial cost of investing in robotic welding technology may be high, the long-term savings in labor costs, reduced errors, and increased productivity make it a cost-effective investment for many manufacturing facilities.
Speed Up The Air Moves
One way to increase the speed of a welding robot is to speed up the air moves. The air moves refer to the robot’s movements between welds, which are controlled by air pressure. Robots typically measure air move speed in a percentage with 100% being top speed for air moves. By increasing the air move speed, the robot can move faster between welds, reducing the amount of time needed to complete a weld cycle.
Keep in mind that increasing the air move speed too much can have a negative impact on the quality of the weld. Higher air move speeds can cause the welding torch to move too quickly, which can result in missed welds or less precise welds. It’s crucial to find the right balance between speed and accuracy to ensure that the finished product is of the highest quality.
Adjust The Part Clearance Spacing
Another way to speed up a welding robot is to adjust the part clearance spacing. Robots go to the exact same spot and follow the exact path every time, so moving the air move points closer to the fixtures, clamps, or other parts can save time. By reducing the distance that the robot needs to travel between welds, the overall cycle time can be reduced, allowing the robot to complete more welds in less time.
However, it’s important to make sure that the part clearance spacing is adjusted carefully to ensure that the welding torch doesn’t collide with other parts or fixtures. Collision can damage the robot or the part being welded, resulting in costly repairs or replacement.
Modify The Order Of Welds
As we mentioned earlier, robots follow the exact same path every time they weld. By starting on one side of the part and working towards the opposite side, we can save time and reduce cycle times. This approach is based on the concept that the quickest way to get somewhere is in a straight line. By reordering the welds, we can make sure that the robot moves in a straight line, reducing the time it takes to complete each weld.
Another way to modify the order of welds is to arrange them in groups based on their size and complexity. By tackling the larger, more complex welds first, the robot can work on them without the risk of collision or interference from other welds. Once the larger welds are complete, the robot can then move on to the smaller, less complex welds.
Embracing Robotic Welding For Increased Efficiency & Profitability
Robotic welding has numerous benefits for manufacturing facilities. It increases accuracy, consistency, and productivity, while also reducing the need for rework. It can also improve safety by welding in environments that are dangerous for human workers.
To make the most of robotic welding, it is important to understand the physiology of automation and how it can be demoralizing to workers if not used properly. Operators should have 1-minute worth of work while the robot is doing 1-minute worth of work, and factories have seen increased production rates by actually slowing down their equipment to match operator speeds.
It is also important to know your parts and double-check that the robot isn’t taught a weird path or a slower speed on purpose. Speaking with the appropriate parties such as engineers or robotic programmers who originally wrote the program can help ensure that the robot is working optimally.
Finally, to increase efficiency and generate more profit, we must focus on increasing robot speeds and decreasing cycle times. We can do this by adjusting the air move speed, modifying the part clearance spacing, and modifying the order of welds. By implementing these strategies, we can make the most of our robotic welding systems and stay competitive in today’s manufacturing landscape.
Arc Solutions: Your Trusted Welding Robot Expert
Looking to streamline your welding processes and increase productivity? Look no further than Arc Solutions, Inc! Our team of robotic welding specialists has the knowledge and expertise to keep your facility operating at unparalleled efficiency. From reducing wasted motions to faster turnaround times, we can help your team work more efficiently and effectively.
But we don’t just stop at improving your current processes. We also provide turn-key solutions to meet and exceed your fabrication needs. So whether you’re looking to optimize your existing workflow or implement a brand new system, you’re in the right place.
Don’t wait any longer to streamline production. Contact us today to see how we can help you achieve your goals.
Back to blog