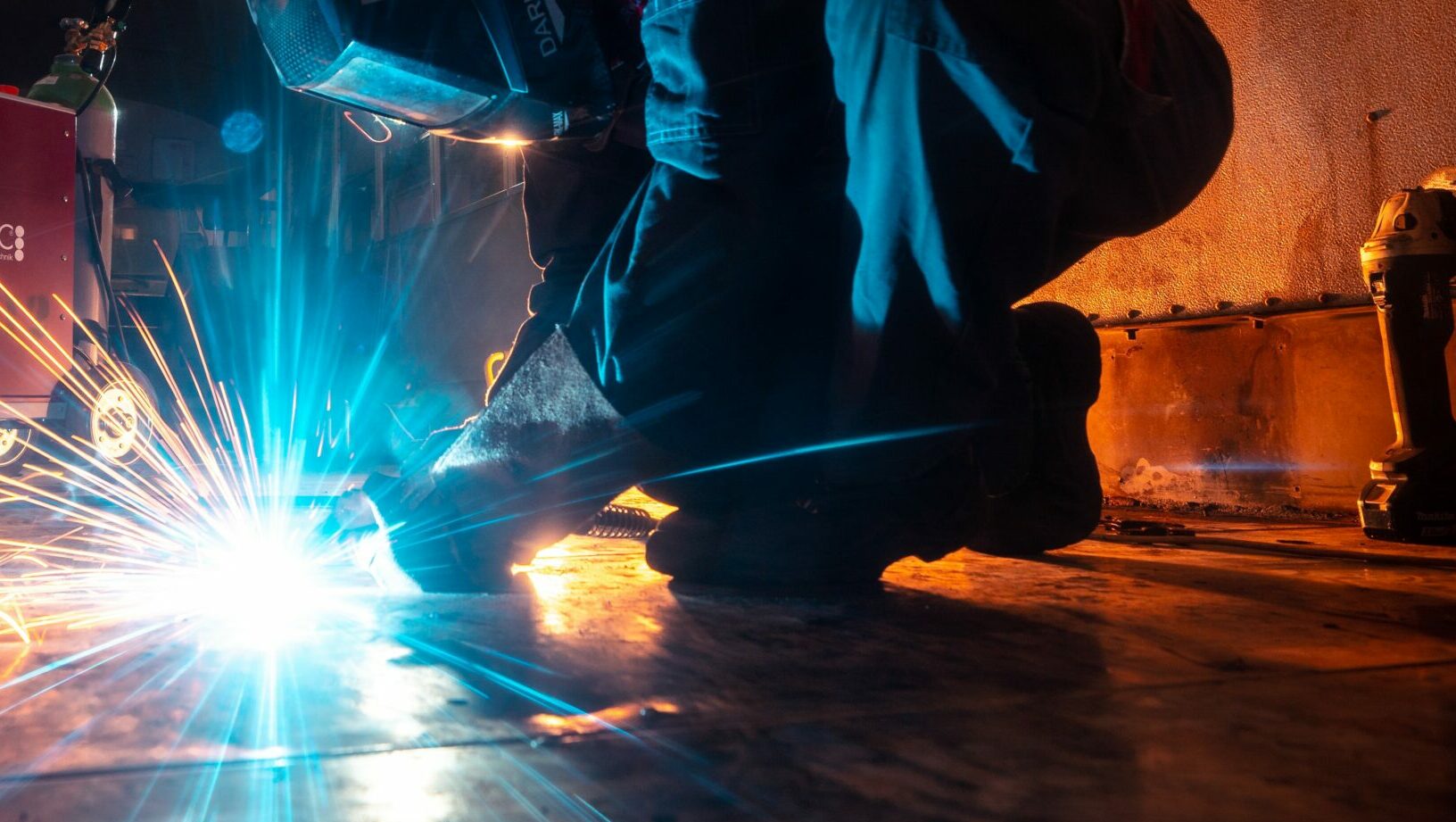
The Power of Change: Upgrading Your Welding Tools
Is it time to upgrade that old faithful welder you bought at an auction over a decade ago? Every company has that piece of equipment they don’t want to get rid of for a multitude of reasons, but is in desperate need of a welder machine repair, or an upgrade. These reasons could be sentimental: an employee’s favorite, fear of change, false belief of cost savings or almost anything else. Let’s take a dive in and see if it’s time to finally pull the trigger and upgrade your tools.
A New Welding Machine Saves You Power And Money
An often overlooked reason to upgrade is reflected in power savings. Let’s use a few Lincoln machines and calculate the power savings of a traditional transformer machine vs. a newer inverter machine. In the chart below, a calculation was done for one production shift of power savings with a new Lincoln Electric inverter style machine (Powerwave S500) and an older Lincoln Electric transformer style machine (CV-400).

When the $4.95 per shift is multiplied out to a full year (estimated 260 working days) this equates to $1,287 per year. When multiplied by 3 shifts that grows to $3,861 cost savings per year.
In addition, many electrical companies will provide discounted rates or rebates for companies who convert to equipment that requires less power draw. If you are switching to newer, more efficient machines this would be a great option to explore.
Improve Your Weld Quality With Advanced Welding Technology
After power savings comes weld quality. Welds that used to be difficult or even impossible may now be very feasible to do. Each manufacturer has their own terminology, but from a high level the general ideas are similar. The benefits of newer equipment include better gap filling, higher deposition rates, more aesthetically pleasing welds (prettier welds), decreased porosity, capabilities to weld exotic materials, different transfer modes to help when welding out of position, and constant penetration. These can be broken down even further. For instance, high deposition rates mean more weld metal gets put down in a given amount of time. It also means that less overall heat goes into the base metal and this helps to minimize distortion.
The advanced waveforms make the welding easier so less technical operators are required. All welding requires is someone who understands the welding process to dial in the parameters. However, once the new machines are dialed in, they weld a wide range of thicknesses using the synergic setting. Now the operator is only turning one knob and the machine compensates for the rest. Existing programs can even be saved so that it takes the guesswork completely out of a parameter adjustment. If applicable, the welder can even record the real weld data to save and refer back to in the future.
Save Space And Strain With A New Welder
The size and weight of welders have decreased significantly with technology. Older machines, like the CV-400 weigh in at 383 pounds. The inverter based Powerwave S500 is capable of 25% more output but only weighs 68 pounds. This creates less strain on operators who move their equipment around. It also saves valuable floor space because the footprint of the machine is significantly smaller.
A final tick against the older machines is repair parts. As product lines become older they are no longer supported by the original equipment manufacturer (OEM). If and when the older equipment breaks down, being able to quickly get the machine repaired and back into production becomes difficult.
We’ve Got Your New Welding Equipment!
If you would like to learn more about new welding equipment, reach out to Arc Solutions, Inc. We have technical sales employees who are happy to help educate you on the pros and cons of major industrial welding brands. We will also provide you with a quote to replace your equipment if desired. If you have a welder that needs service work, our team of authorized service technicians will get your machine fixed and back on your floor ASAP. Contact us today to upgrade your welder and your workflow, and shop our equipment in our store!
Back to blog