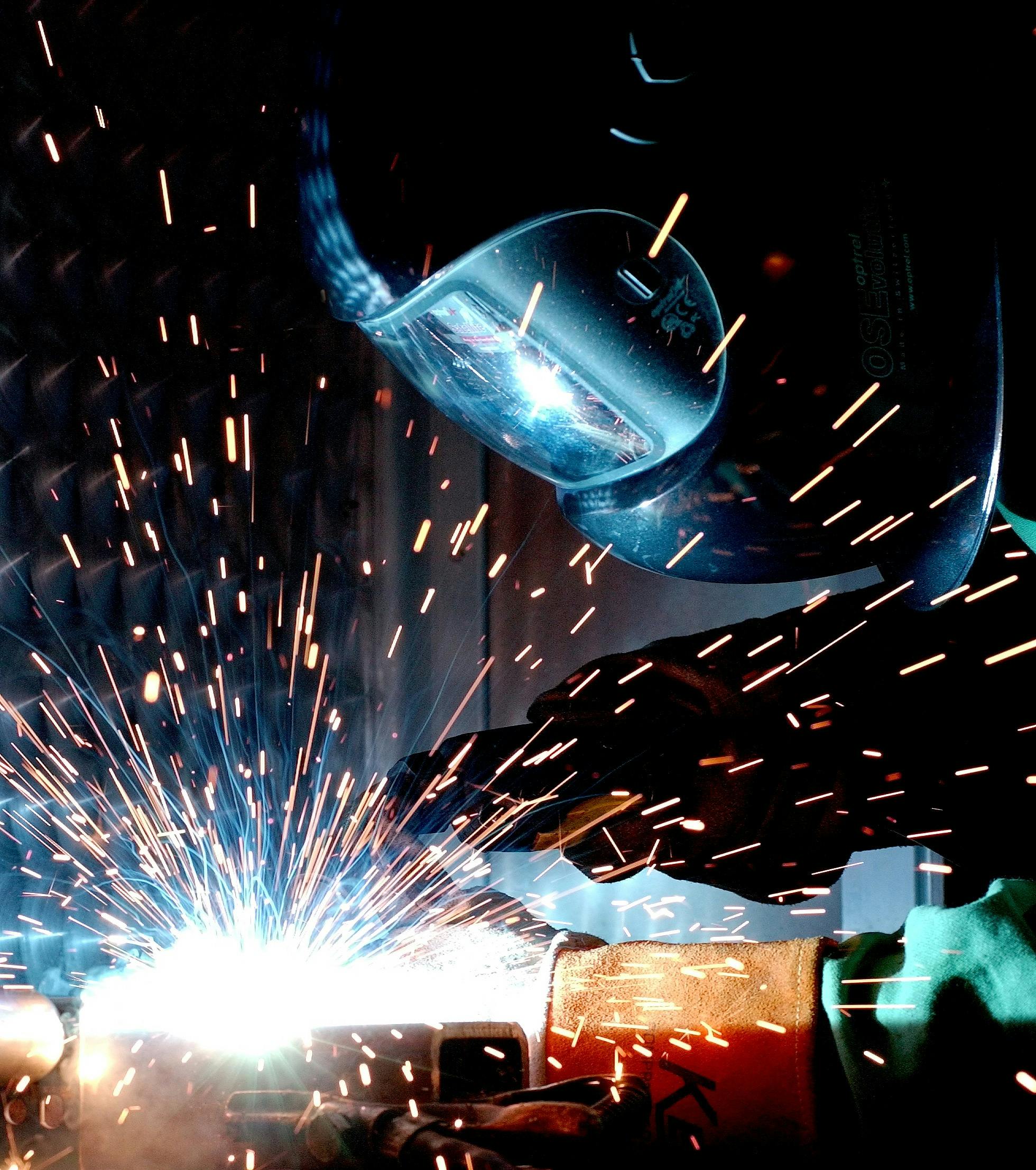
Gas Types Used in Welding: Argon, Acetylene, and Nitrogen Explained
When sourcing gases for welding or cutting applications, understanding the role of shielding gases in different types of welding processes is essential. The right gas can significantly impact weld quality, strength, and efficiency.
This guide outlines the most commonly used welding gases—argon, acetylene, and nitrogen—and compares their uses, benefits, drawbacks, and effects on various welding processes.
Why Shielding Gas Matters in Welding
Every weld must be protected from atmospheric contamination until the metal solidifies. Oxygen and nitrogen in the air can introduce porosity, spatter, and cracking. Shielding gases act as a protective barrier, stabilizing the arc and improving weld integrity. The type of welding gas you choose will determine your results.
Understanding Argon Gas
Argon gas is an inert shielding gas commonly used in both MIG and TIG welding. It provides excellent arc stability and reduces spatter, making it ideal for precise welds and clean finishes.
Applications:
- MIG welding aluminum (requires 100% argon)
- TIG welding all materials
- MIG welding of stainless or mild steel (when blended with CO2 or O2)
Pros:
- Stable arc and low spatter
- Inert—no chemical reactions with molten metal
- Excellent for spray and pulse transfer modes
Cons:
- More expensive than CO2
- Limited penetration when used alone on thicker materials
Using Acetylene in Torch Cutting
Acetylene is most commonly used in oxy-fuel torch cutting and gas welding applications. When combined with oxygen, it produces one of the hottest flames available—ideal for cutting ferrous metals.
Applications:
- Oxy-acetylene cutting
- Brazing
Pros:
- High flame temperature
- Precise control
- Great for portable setups and fieldwork
Cons:
- Flammable and unstable if handled improperly
- Not suitable as a shielding gas for arc welding
The Role of Nitrogen in Welding & Plasma Cutting
While not as commonly used as argon or acetylene, nitrogen is still a valuable welding gas in specific applications. It is often used as a backing gas or purging gas, and in plasma cutting systems.
Applications:
- Plasma cutting
- Purging stainless steel welds
- Shielding in some specialized MIG applications
- Many laser applications (cutting and welding)
Pros:
- Cost-effective
- Inert in many settings
- Helps reduce oxidation in purging
Cons:
- Can cause brittleness if used incorrectly in arc welding
- Not ideal as a primary shielding gas for most applications
Comparison Chart: Argon vs. Acetylene vs. Nitrogen

FAQs: Welding Gas Questions Answered
Can you mix gases? Yes. Gas blends (e.g., 75% argon/25% CO2) are common and tailored to specific applications. For instance, a 90/10 argon/CO2 mix works well for spray transfer MIG welding.
Which gas is best for aluminum welding? 100% argon gas is recommended for both MIG and TIG welding aluminum.
What type of welding gas should I use for stainless steel? For MIG: Try a 98% argon / 2% CO2 mix. For TIG: Use 100% argon.
Is nitrogen ever used in MIG or TIG welding? Rarely, and only in highly specialized processes. Nitrogen is more commonly used in purging or plasma cutting.
Choosing the Right Welding Gas for Your Application
The right shielding gas depends on the material, process, and desired weld quality. Technical buyers need to assess the gas’s role in heat input, arc characteristics, and post-weld cleanup. Whether you’re selecting gases for structural steel, stainless fabrication, or high-precision aluminum work, the type of welding gas directly affects your results.
Explore welding gas options compatible with our full line of welding products—we’re here to help you find the right solution for every application.
Back to blog