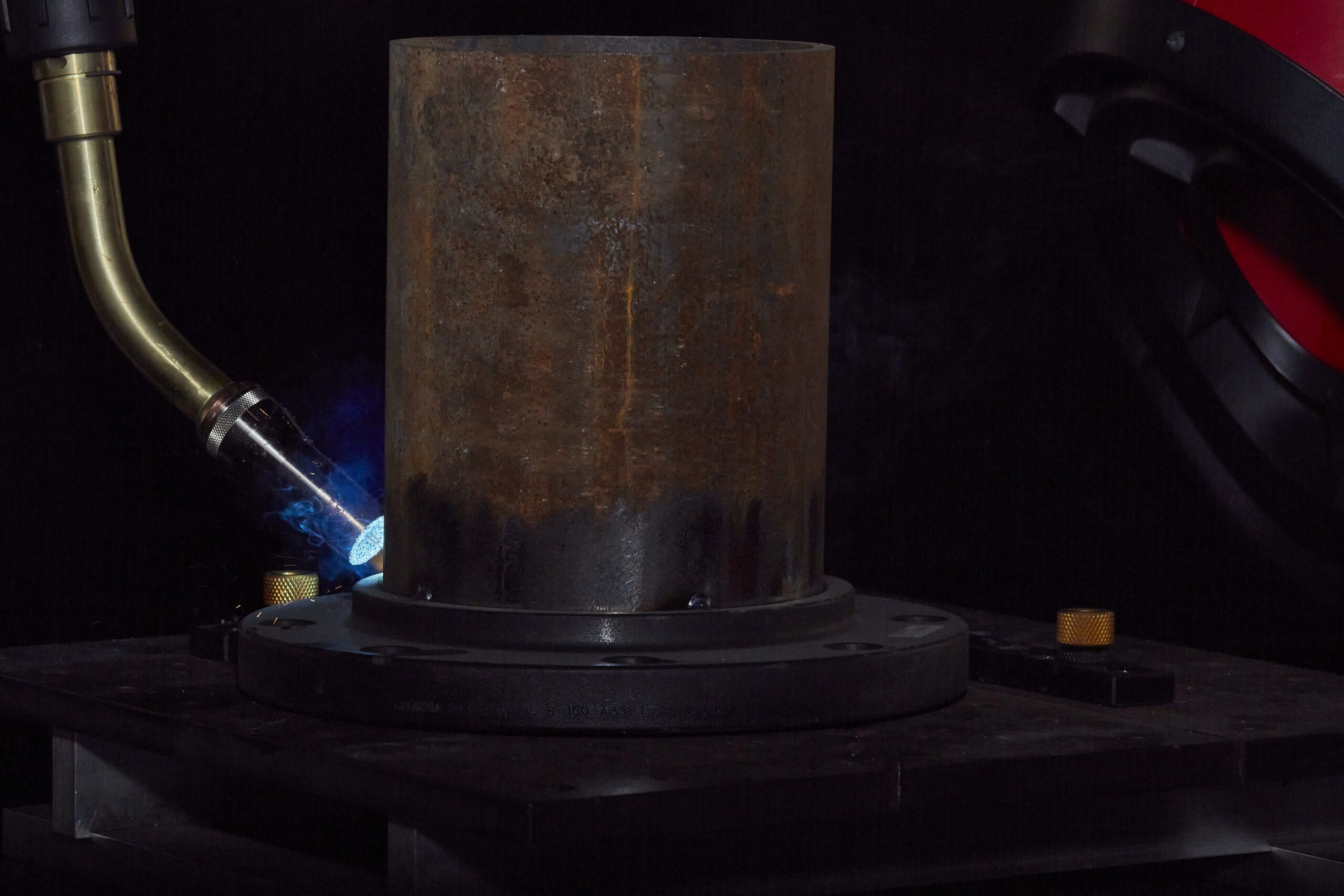
How Cobots Are Changing the Game in Manufacturing
Automation is changing the world all around us. Manufacturing is one of the industries in which automation has had the most impact. There are many different automated routes a manufacturer can go down. One of the newest and fastest-growing automations is collaborative robots, including the Lincoln Electric Cobots.
Cobots, or collaborative robots, are designed to collaborate with human assistance. The idea of most automation is to increase productivity while maintaining quality. How do manufacturers do these things and what does it consist of? The answer is simple: resources, money, and time! The three components are connected so improving in one area tends to have a domino effect.
Who Can Benefit From A Cobot?
Before diving too deeply into what a Lincoln Electric Cobot has to offer, let’s talk about who would best benefit from a Cobot. A Cobot is certainly not a one-type-fits-all piece of technology. Since cobots work in collaboration with you, they are designed with safety in mind. Cobots move slower than traditional robots with a max speed of 250 mm/second. When compared to a traditional robot in a time cycle analysis, a Cobot will tend to have increased cycle time. However, the weld time will remain the same since both cobots and robots weld at the same weld travel speed.If you’re not mass manufacturing a single part non-stop but rather have 20-50 parts of multiple different items you interchange, a Lincoln Electric Cobot could be a good fit for you. When operating with a traditional robot, running these mass amounts of one item and then switching to another item significantly affects production rates and downtime. The time to switch out all the necessary components and reprogram the machine becomes expensive fast. The cobot controller has the capability to store hundreds of programs so once that program is written it is easy to call it back into production. You can also “call” multiple programs into a master program enabling you to weld different parts or designs inside the same robot program.
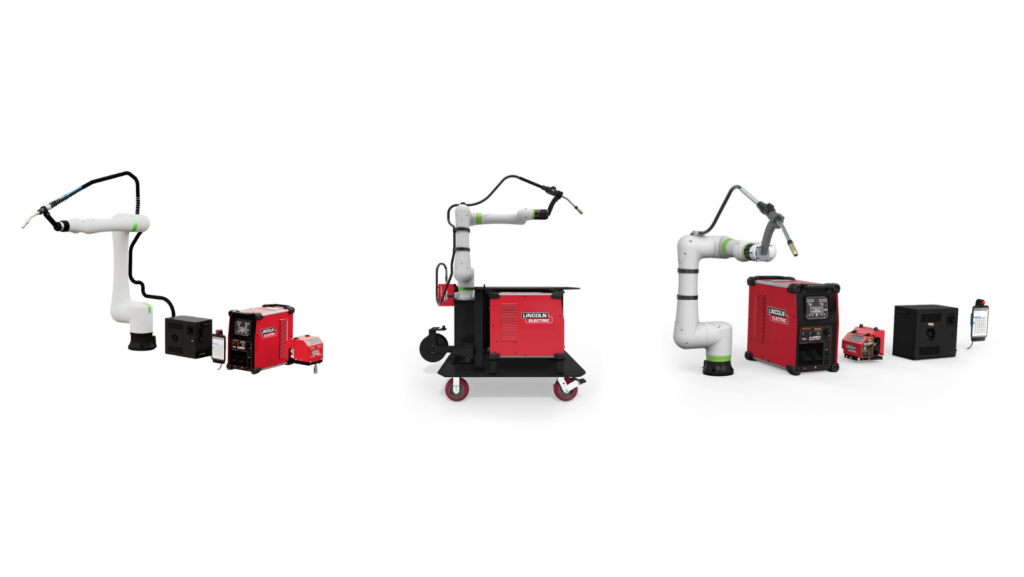
Resources
As previously mentioned, cobots were created with human collaboration in mind. To the worker, a Cobot could be considered a coworker. Cobots are often advertised as an ‘anyone can do it’ piece of technology. However, there is a necessary minimum amount of knowledge in the field you work in required to operate the equipment. It is important that your cobot programmer knows how to manually weld and is also comfortable with a smartphone. Another important quality is your controller needs to have a clear vision of the desired results and a general understanding of what it takes to achieve your end product. While not for just anyone off the streets, the teachability of Lincoln Electric Cobots is still one of its largest selling points. If you combine the general understanding I touched on previously with the teachability of the Cobot, your likelihood for success is significantly more feasible.
If we look at resources from another perspective, a Cobot (like any robot) is designed to increase efficiency. This isn’t only from a time standpoint but also from a production perspective. When a Cobot is taught a task its job is to complete the task as taught. This functionality results in fewer mistakes and more consistent work, which maximizes your use of physical resources For example, a MIG weld wire using pulse waveforms has a 98% process efficacy. This means 98% of the weld wire purchased actually makes it into the weld rather than spatter on the fixtures or shop floor. Taking this a step further, this maximizes your output as well.
There tends to be a negative connotation associated with robots and Cobot automation in general. However, taking the time to understand the functions and purpose behind the technology can help alleviate these concerns. As mentioned previously a cobot is a collaboration robot. It is not designed to take the place of the worker; it is designed to be a resource for the worker. The best part is that Lincoln Electric Cobots are customizable – we work with you to get the setup you need.
Time
The next area of productivity is time and this is an obvious point of discussion with any form of automation. One of the greatest leaps the manufacturing world can take when increasing productivity is streamlining operations as much as possible. The idea of having a seamless flow from one operation to the next is the ideal pathway for any manufacturer. For streamlining operations, cobots can be a pivotal resource, as the production rate of a robot is typically triple that of a manual welder. The repetitive and consistent nature of a Cobot makes for a process to be completed from the starting teach point to the finishing teach point the same way, every time. Since the Cobot is busy doing the actual welding, the operator now spends their time loading and unloading parts. Using a Cobot is like picking up an employee who also happens to be the fastest welder in your shop.
A Cobot allows companies to explore new technology, refine existing processes, and push the boundaries of what is possible in manufacturing. This equipment is not only a resource for improving productivity but also a catalyst for innovation and progress.
Money
It is no secret that when time is saved, money is also saved! As mentioned in one of our previous blogs, “The typical labor and overhead cost is three times the hourly wage of the employee, meaning that a $20/hr employee costs the company $60/hr to have on staff.“ In areas where operations can be streamlined, resources optimized, and downtime minimized, money can be saved. These benefits rank among the first improvements you’ll see that help prove your return on investment. Additionally, its collaborative design eliminates the need for expensive safety measures and dedicated robot zones, further reducing capital expenditures. Another bonus with the Lincoln Electric/Fanuc Cobots is that you’ll always have access to the latest software updates; as these are FREE and available online – keeping your production a step ahead of the game.
Find The Perfect Cobot With Arc Solutions!
Technology never slows down and is in a constantly evolving state. The Cobots designed today will continue to adapt to the needs of the industry and we are ready for it. The dynamic role of collaborative robots in enhancing manufacturing environments cannot be overstated. From improving safety and productivity to fostering innovation and adaptability, cobots are redefining the way we think about manufacturing. As we embrace this collaborative future, one thing is clear: the era of cobots has only just begun, and the possibilities are limitless. If you’re interested in finding out if a cobot is the best fit for you contact us to schedule a demo today!
Back to blog