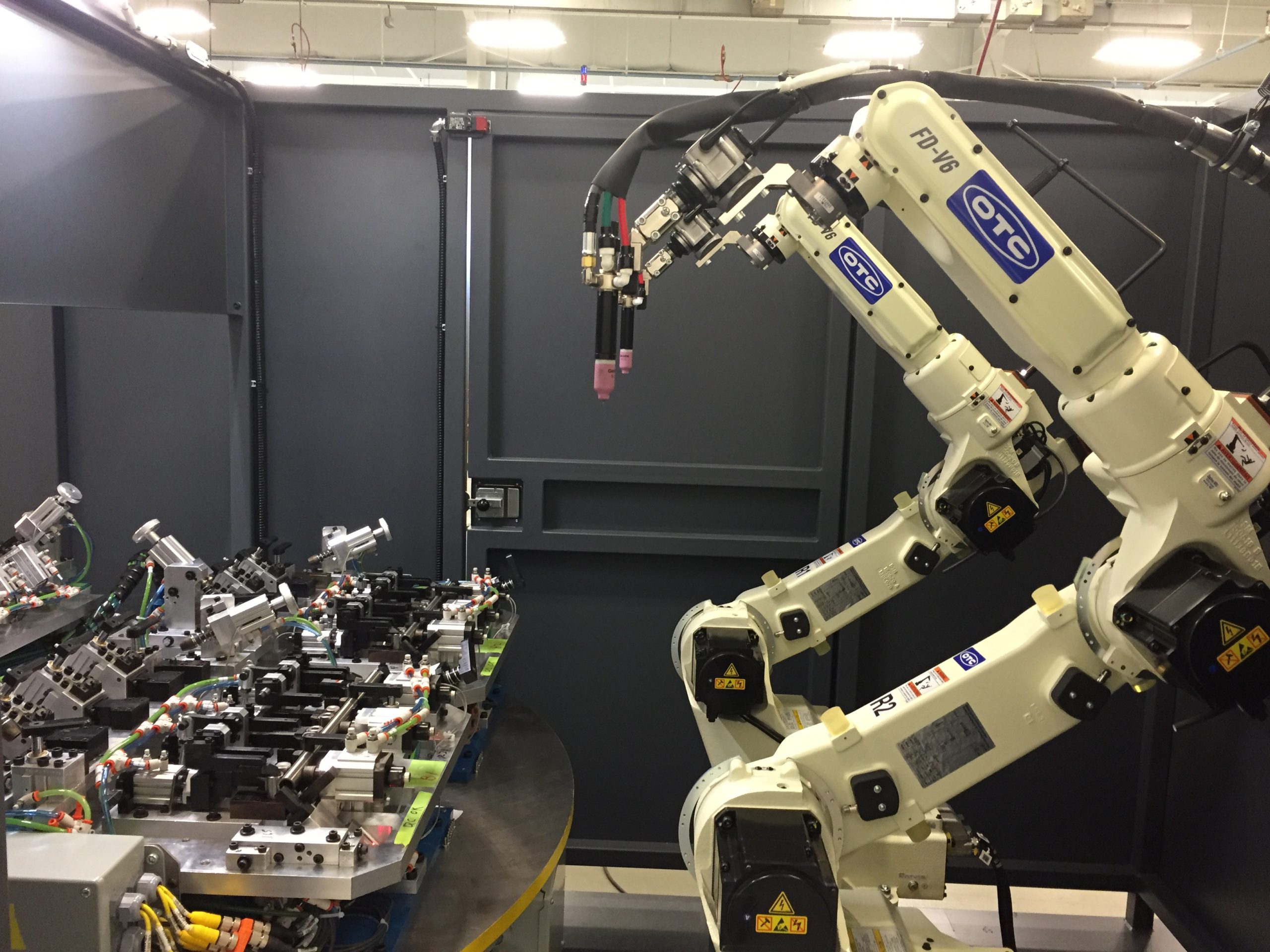
Why You Should Be Automating Your Welding Process
There’s no question that the employment crisis of 2021 is impacting every industry on the market – including finding professional welders.
Many manufacturers are seeing the crisis as just that, a crisis. In all reality, they should be viewing this as an opportunity to automate day-to-day welding processes that ultimately boost production levels and keep costs down.
In other words, the “labor shortage” is actually just an opened door to make a strategic business move that moves the needle for years to come.
With all of that said, is automation the right solution for today’s market? There are many benefits of automated welding. It eliminates the need to interview, hire, and train new employees because it all comes down to a one-time programming session that provides high quality results without sacrificing time and budget.
This article highlights why welding automation is critical. But first, it’s important to understand
What Is Welding Automation?
Over the last 20 years, Arc Solutions has passed down the best welding techniques to make every project a success. While manual welding capabilities is an admirable trade, the demand for such a skill has outgrown the number of skilled workers willing to do it, thus forcing technology improvements. As a result, our extensive inventory of welding equipment and machine repair services have also adapted to serve the needs of today’s modern market – especially when it comes to automated welding equipment.
But what does it mean to automate welding processes in the first place?
Also known as robotic welding, automated welding equipment introduces a game-changing advantage to your manufacturing process. With just one specialized machine, you streamline the workload of several employees. Job turnaround time is cut in half and the risk of human error is completely eradicated. Welding automation is a lot more than fancy equipment. The benefits of upgrading your resources goes far beyond the shop and drastically improves the final product.
The Benefits Of Automated Welding
Any manufacturing plant or contractor looking to profit from streamlined production should consider automated welding equipment. After all, who wouldn’t want to simplify this complex process? If you’re unsure about whether automated welding can benefit your business, keep the following points in mind:
Unparalleled Product Quality
Incorporating robotic welding equipment into the mix enhances the integrity in which your welded products are made. Manual welding is limited when it comes to quality control. This is because welds can only be made once and any mistakes made along the way are easily noticed. With the help of automated processes, potential mistakes like these are reduced, resulting in a much more superior product than traditional manual welding can accomplish.
Enhance Project Capacity
Humans can only take on so much work. We have capacities that are quickly exhausted and regulated by work breaks, shifts, and general productivity levels. In other words, automated welding equipment surpasses the capabilities of manual welding because our tools don’t need to clock out for a lunch break. Streamlining your production with robotic welding equipment keeps everything moving consistently while simultaneously empowering your bandwidth to take on more projects.
Reduced Production Costs
Automated welding not only enables higher project capacity, but has shorter cycle times. As a result, the cost to complete projects is minimized. This goes hand in hand with condensing the amount of mistakes that are made during a weld. Robotic welding is designed to decrease fatigue induced errors – ultimately cutting back on the amount of material needed to finish the job correctly
Safer Working Environments
It goes without saying, but a work environment is always safer when less people are on the floor. Robotic welding arms and tools require supervision to a certain degree, but are programmed to weld on their own. Manufacturing plants also benefit from not needing the protective welding gear like goggles and gloves to keep employees out of harm’s way.
Robotic Welding: The Key To Efficient Manufacturing
Despite the labor shortage the media keeps putting in our faces, there are upsides to less people working. Manufacturing plants, contractors, and DIYers can all benefit from robotic welding equipment in more ways than one. Not only does automated welding give you optimal control over product quality, but using robotic welding machines keeps costs low, uses less scrap, and cuts back on the need for providing protective welding gear.
Purchase Your Automated Welding Equipment Today
Any smart business owner can argue the benefits of automatic welding. Arc Solutions is on standby to answer your questions and help find the right solution for your welding needs. We’ve been doing this for a long time and are experts in showing our customers the best tools to refine production and upgrade performance.
Talk to a local team member today to get started.
Back to blog